You may be lean but are you green?
In today's evolving business landscape, the term "lean manufacturing" is commonplace. It is a pivotal concept celebrated for driving organisational success. A business model that prioritises activities customers are willing to pay for, while considering everything else as waste. Defined by its focus on managing and reducing waste, lean manufacturing seems, at least on paper, to address sustainability goals, but is lean enough?
What is lean manufacturing?
Emerging from the post-war 1950s through the Toyota Production System (TPS), lean manufacturing is built upon the concept of continuous and incremental improvements in both product and process. Its primary objectives are to reduce production time, improve responsiveness from suppliers and to customers, enhance product quality, and boost efficiency. This is achieved by eliminating, simplifying, reducing, or integrating activities that do not add value to the business, i.e. effectively managing and minimising waste.
Toyota identified 7 types of waste (Muda) in a business:
- Over production: producing products before a confirmed order.
- Unnecessary waiting: inactive work periods leading to lengthened cycle time which reduces agility and responsiveness.
- Unnecessary transportation: unnecessary movement of people and goods inside the system.
- Overprocessing: processes that are more complex than required or making parts beyond the standard expected by the customer.
- Unnecessary inventory: an excess of raw materials, work-in-process elements or finished products.
- Unnecessary motion: inefficient layout or automating processes before improving the method.
- Too many avoidable defects: poor quality output that needs correction.
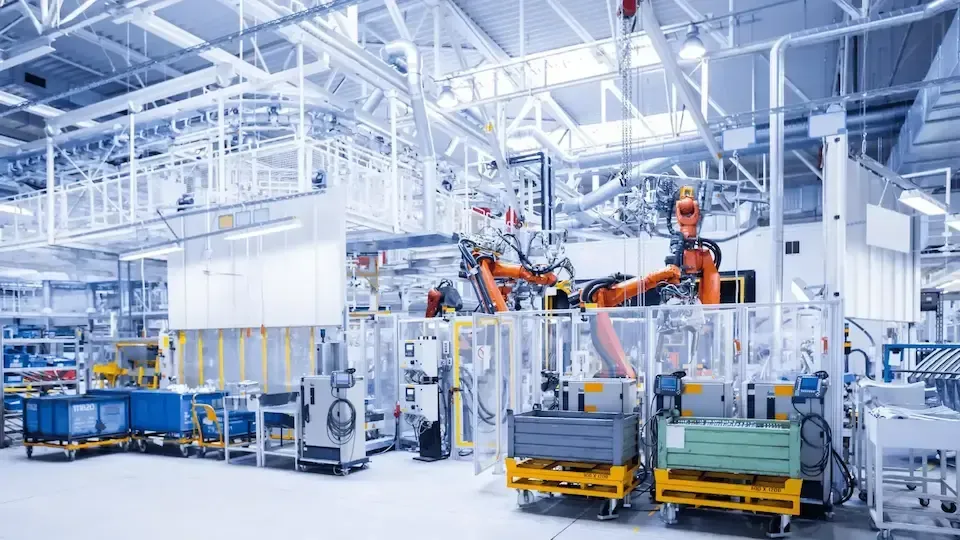
At its core, lean manufacturing embodies the relentless pursuit of efficiency and waste reduction across all facets of production. By eliminating unnecessary inventory, minimising lead times, and optimising workflows, businesses can achieve significant cost savings while boosting product quality and customer and employee satisfaction. Lean methodologies foster a culture of continuous improvement, empowering employees to identify and address inefficiencies proactively.
Key areas where lean business practices are commonly applied include:
- Supply chain management
- Production processes
- Inventory control
- Quality assurance
- Workforce optimisation
- Customer relationship management
Lean principles drive efficiency and promote agility, helping businesses to respond swiftly to changing market dynamics and customer demands. From small and medium sized businesses through to multinational corporations, the adoption of lean manufacturing methodologies has become synonymous with operational excellence and growth.
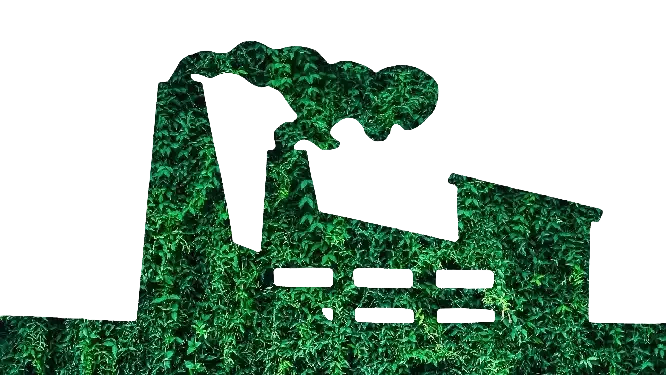
How is green manufacturing different to lean manufacturing?
Green manufacturing (also known as sustainable or eco-friendly manufacturing) prioritises economically efficient procedures that also minimise the environmental impact of both the manufacturing process (using resources more efficiently, lowering energy consumption and reducing waste generation) and the complete life cycle of the product, from design through to disposal. It incorporates all the benefits of lean manufacturing, but with additional green credentials – highly attractive to customers, investors and current and future employees.
In short, the main distinction between green and lean manufacturing lies in their intent: green manufacturing strives to minimise the environmental impact, whereas lean manufacturing aims for maximum efficiency.
Embracing sustainable manufacturing
Green manufacturing embodies a holistic approach to production that prioritises environmental stewardship, social responsibility, and economic viability. It encompasses the integration of eco-friendly practices, renewable resources, and ethical labour standards to minimise ecological footprint and promote long-term sustainability.
Sustainable manufacturing initiatives vary from the straightforward and easily implementable measures to comprehensive and complex overhauls requiring industrial project management:
- Encouraging employees to turn off equipment when it’s not being used.
- Installing motion sensors to lights and self-closing taps in bathrooms.
- Reusing materials currently discarded as waste.
- Switching to renewable energy sources.
- Using recycled/ recyclable materials in the manufacturing process.
- Replacing equipment to more energy-efficient alternatives.
- Procuring and installing specialist equipment to meet ongoing HSE and compliance requirements.
- Reviewing the practical and economic implications of renewable thermal energy options to futureproof a business.
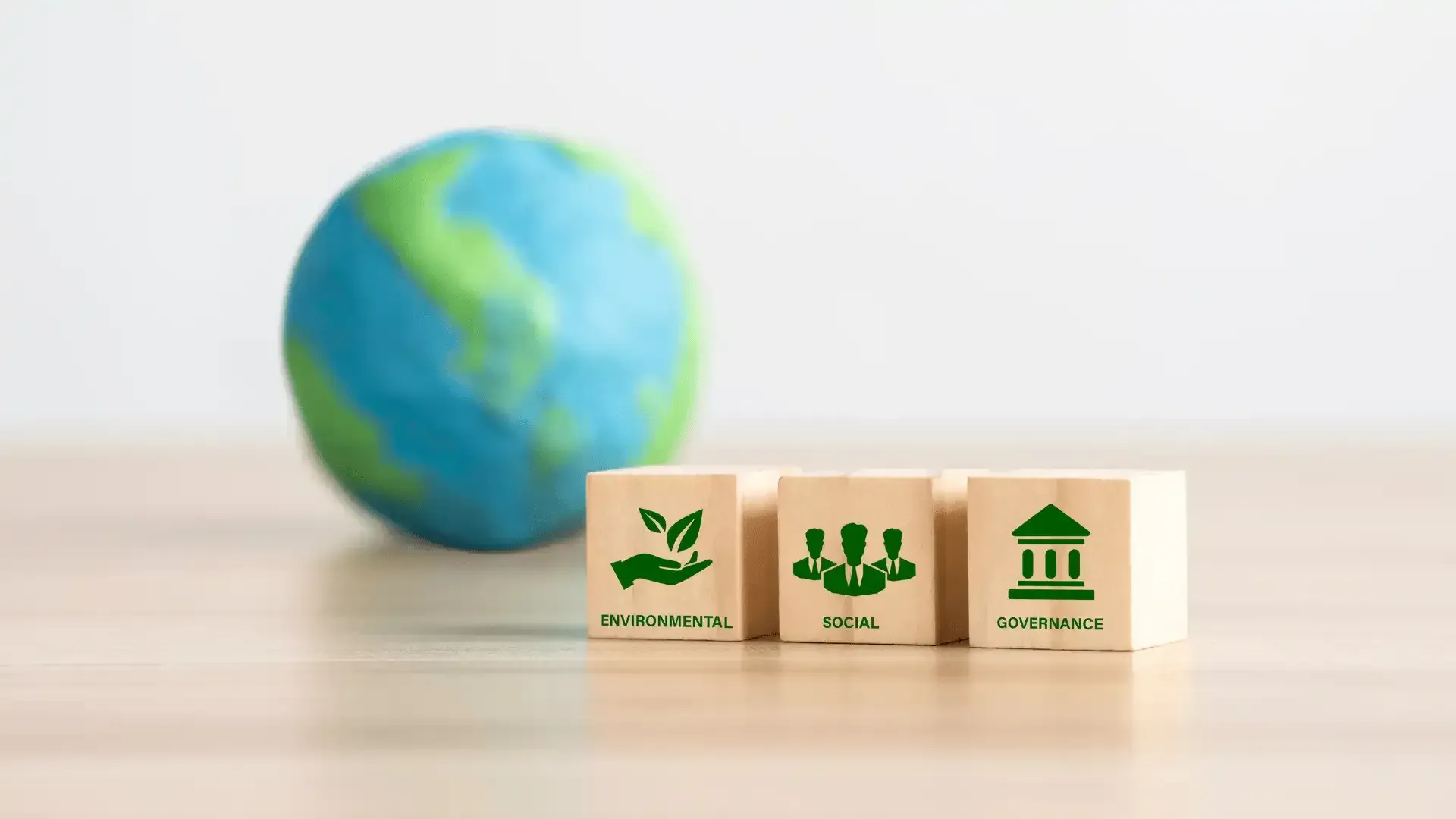
The benefits of transitioning towards sustainable manufacturing practices extend beyond environmental preservation; it's about creating shared value for stakeholders while safeguarding the planet for future generations. Integrating sustainability into core business strategies fosters innovation, drives competitive advantage, and breeds long-term resilience in an increasingly uncertain world. By embracing green business practices, businesses mitigate operational costs, enhance brand reputation, and capitalise on emerging market trends favouring sustainability.
Areas within an organisation ripe for green business practices include:
- Energy management and efficiency
- Waste reduction and recycling
- Water conservation and wastewater management
- Sustainable sourcing and supply chain transparency
- Emission reduction and carbon footprint management
- Stakeholder engagement and community outreach
Bridging lean and green: the path to holistic optimisation
The comparison between lean and green manufacturing concepts also reveals their complementary nature and overlapping aspects:
- Both emphasise resource productivity in manufacturing by reducing waste and emissions and promoting efficiency in production steps.
- Employee involvement and training are vital for continuous improvement in both concepts.
- Both require changed mindsets and company cultures supporting their underlying philosophies.
Integrating lean methodologies with sustainable manufacturing practices, enables organisations to unlock industry competitiveness and access new collaborations which amplify the environmental impact and drive meaningful change across the entire value-chain.
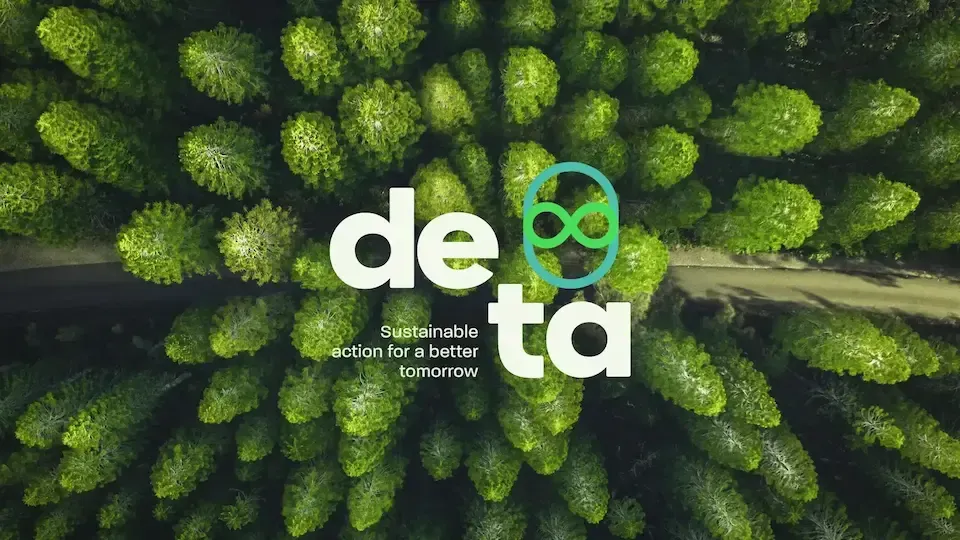
How can DETA help your business be lean and green?
The merging of lean and green principles represents a paradigm shift in contemporary business practices, surpassing traditional notions of efficiency and profitability. As businesses navigate the complexities of a rapidly changing world, embracing sustainability isn't just moral —it's a strategic imperative, and this is where DETA can help you.
DETA’s energy consultants in New Zealand and Australia play a pivotal role in business transformation. We appreciate the prospect of changing how your business operates can feel overwhelming, which is why we are with you every step of the way. Once we’ve identified and explored any inefficiencies in current working practices, we create and deliver a Sustainability Roadmap to pave the way for a more sustainable future—one that exploits the economic prosperity of lean manufacturing with the environmental stewardship and social equity of green manufacturing.
We look at your business holistically so we can implement the most effective energy-saving initiatives and develop comprehensive carbon reduction strategies tailored to your unique operational needs. We’re firm believers in making life as easy as possible for our clients, which is why we have an inhouse multidiscipline team of experts for both excellence and consistency.
Whether you require an energy audit and management, need advice from our wastewater consultants to ensure compliance with regulatory standards, or crave the guidance and invaluable insights from DETA’s sustainability consultants, you can unlock new opportunities for growth, resilience, and competitive advantage.
If you would like your business to be involved in positive change for a greener future, call DETA today, click here for contact details for our Aotearoa New Zealand, Australia, and the Pacific teams.