Energy Audit & Decarbonisation Pathway led by DETA - Cheetham Salt AU
DETA & Cheetham Salt - Decarbonisation Pathway
DETA partnered with Cheetham Salt to revolutionise site energy consumption and achieve organisational sustainability. Cheetham Salt, being the largest producer and refiner of solar salt in Australia, approached DETA requesting an Energy and Carbon Roadmap to transition their sites to net-zero carbon and integrate sustainability plans across their entire organisation.
Both the Energy and Carbon Roadmaps set out pathways to potential emission and energy reductions. Specifically identifying opportunities and projects that will contribute to overall reduction targets and goals.
The DETA team began by completing an audit of Cheetham Salt, assessing existing energy consumption and carbon emissions. DETA conducted an energy audit to AS3598.2:2014 standards where the team had the opportunity to explore cutting-edge initiatives that guarantee a return on investment within 1 to 3 years. Production processes were also analysed to identify potential energy reduction initiatives as well as energy demand and fuel switching possibilities. DETA then discussed future plans, assets and opportunities with Cheetham Salt in order to deliver comprehensive and valuable Energy and Carbon Roadmaps.
The project was broken up into four primary deliverables.
A comprehensive report - detailing the energy consumption and carbon emissions baseline of Cheetham Salt
Specific recommendations - for energy reduction initiatives and efficiency improvements at all operational levels
Energy transition roadmap - outlining the steps, actions, and timeline for achieving Cheetham Salts carbon neutrality goal
Technology assessment - identifying opportunities for reducing carbon emissions and improving energy efficiency
The DETA project delivery team worked alongside Cheetham Salts group sustainability coordinator, Kshitija Katkar, as well as a range of other key contributors within the Cheetham Salt business.
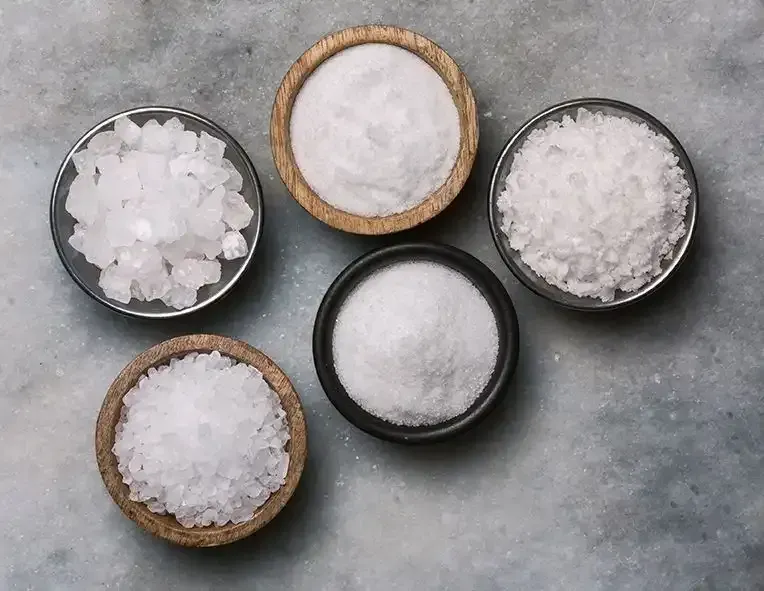
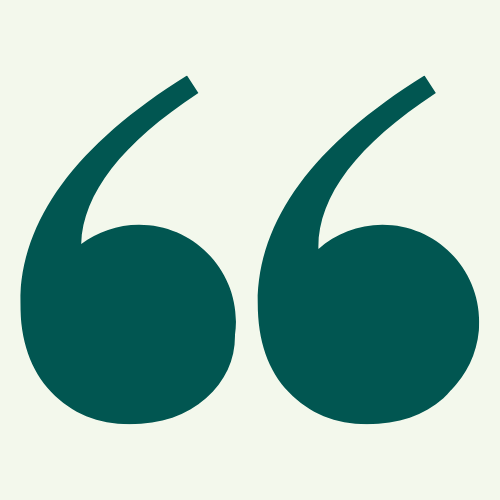
We were thrilled to work with the DETA team. Their work on this project has enabled us to gain a comprehensive understanding of our energy consumption and has identified a range of priority demand reduction opportunities for our site. DETA also completed an investigation which provided a transition plan to decarbonise our operations. Sustainability is at the core of Cheetham Salt’s culture, and after completing this work with the DETA team we have a practical roadmap to implement sustainable solutions on energy & carbon, ensuring a greener footprint for our business.” - Kshitija Katkar
The project delivery phase presented some unique challenges to the DETA team. Due to the corrosive nature of salt the longevity of equipment was comparatively lower to other industries, thus affecting the return on investment (ROI) for energy reduction initiatives. Despite this challenge the DETA delivery team were determined to find innovative solutions and strategies to optimise energy efficiency and mitigate impacts of corrosion on equipment.
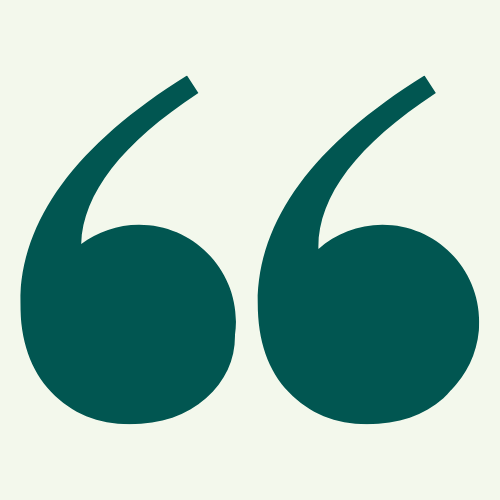
Glenn Schultz, DETA Business Development Manager (Australia), said “Cheetham Salt was willing to push the boundaries of traditional thinking, understanding salt refining in a decarbonised economy requires forward innovative action. Our work on the Price site will now be rolled out to the rest of the organisation. "There are significant decarbonisation challenges in solar salt refining, such as transition strategies for heavy fleets in corrosive environments, large pumping transfer stations working off remote electrical network settings, & the unique impacts the corrosive environment has on ROI for energy reduction initiatives. Despite these challenges, we were determined to find innovative solutions and strategies that would optimize energy efficiency.”
The final report served as a catalyst for the board to make informed decisions and implement strategic initiatives that align with sustainable goals. It provided concrete data, recommendations, and a clear roadmap for integrating sustainable practices into various aspects of the organisation. By DETA providing expert energy audit services and delivering a comprehensive energy transition roadmap, Cheetham Salt gains a competitive advantage, enabling significant cost savings, positioning the company as a leader in sustainability, and attracting environmentally conscious stakeholders.
The DETA team were able to identify Carbon savings of 4,033 tCO2e/year which is a 96% reduction from current emissions.
By collaborating on projects with businesses such as Cheetham Salt that are committed to integrating sustainable practices into their core business models, DETA can work towards achieving our strategic goal of removing 2 million tCO2 emissions every year by 2030. DETA can help you make a positive difference in climate action by providing the support you need to start your decarbonisation journey.